The successful development of each project’s enclosure system design includes effective communication of engineering and performance strategies to clients, contractors, and executives. Two-dimensional drawings and renderings may not convey the design elements which lay beyond the surface.
Enter – the 3D print.
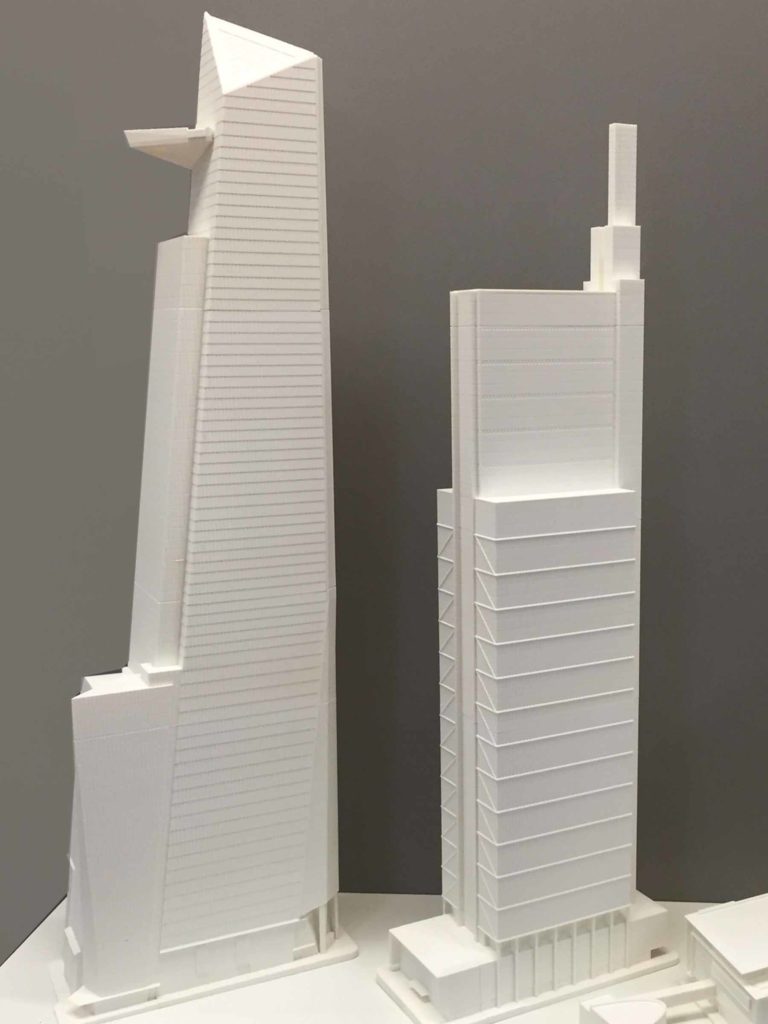
3D prints of 30 Hudson and Comcast Technology Center.
Prototyping in the Design Process
Three-dimensional full-scale reproductions offer a tactile and visual engagement that cannot be achieved without the physical model. Such prototypes also allow the design team to experiment with new ideas and numerous design iterations up-front avoiding costly oversights further into the project. A bolt assembly can be printed in hours, or a vertical mullion extrusion overnight. The physical model is more than a visual mockup – the printed form acts as a functioning assembly with pieces able to snap together and verify design tolerances.
The most common prototype developed early on is of the stack joint. The significance of this location is it is where four units intersect, the units anchor back to primary structure, and where considerations for movements such as live load deflection, thermal expansion, and seismic movement are accommodated. Aesthetically, this joint garners attention as it is typically the largest joint within the envelope system.