By Dan Bettenhausen, Director of Mechanical Engineering & Adam Krueger, Mechanical Engineer
This is the third installment in our series exploring advances in glazing products and their role in enhancing building envelopes’ thermal performance and sustainability. In parts one and two, we covered conventional insulated glass, the evolution of coating technologies, multi-pane glass, and dynamic coatings—products that are either widely used or rapidly gaining traction. Here, we focus on two transformative technologies still emerging in U.S. curtainwall design: vacuum-insulated glazing (VIG) units and building-integrated photovoltaic (BIPV) glazing. While these technologies are not new, evolving energy codes and a growing emphasis on sustainability have brought them to the forefront. VIGs offer the potential to improve insulation performance significantly and are particularly suited for facade retrofits. Meanwhile, BIPV glazing holds promise for achieving net-zero energy buildings by integrating energy generation directly into the facade.
History of Vacuum Insulated Glass
As it applies to developing new insulating materials, the study of heat transfer has long entertained the prospect of evacuating gasses from voids within a given media to improve its insulating properties further. Intuitively, heat conduction within a gas, which arises from molecular collisions and vibration, cannot occur in a vacuum, leaving thermal radiation as the only mode of heat transfer. Many insulating products are limited by the thermal conductivity of a given gas, such as air, entrapped in a lattice of fibers. Two practical problems commonly arise in the design of “real world” vacuum insulation products. The first considers the long-term resilience of seals required to isolate the evacuated region from atmospheric pressure. The second entertains the means necessary to prevent the cavity walls from collapsing due to the gauge difference in pressure.
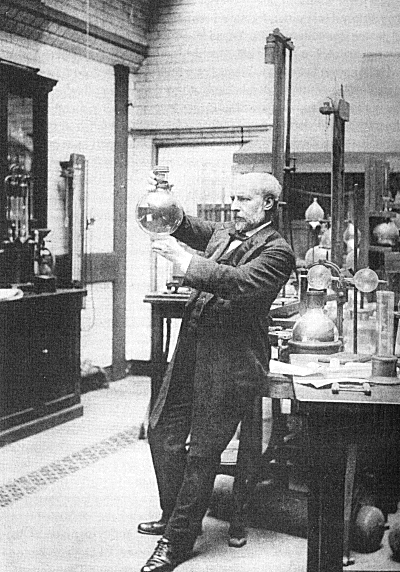
As early as 1892, Scottish Scientist Dewar employed evacuated double-walled flasks to preserve nitrogen in its liquid state, and his name is still credited to vessels of this design1. The ubiquitous vacuum, “Thermos,” was first prototyped in 19032. The first proposed use of vacuum insulation in a window is credited to German Scientist Zoller, who patented the concept in 1913 without producing a successful prototype3. Various theoretical concepts echoed this effort over the next seventy-five years, but it was not until 1989 that Robinson and Collins would produce a viable physical assembly4. At this time, research in vacuum insulation was again “in vogue,” citing concerns over the use of CFCs in conventional insulation products and in response to the recent oil crisis. The effort began a year prior. Stephen Robinson was completing his undergraduate work as a physics student at the University of Sydney under the mentorship of Richard Collins. He received an award for his senior undergraduate project, demonstrating that glass plates could be soldered in a vacuum to produce an insulating effect. This process was then refined as the two continued their collaboration. A step in the manufacturing process was included to outgas the materials by introducing a second stage of heating, and a glass tube was introduced to evacuate the air cavity5. This work was presented at the 1989 International Solar Energy Society (ISES) congress in Kobe, Japan. In 1994, the Nippon Sheet Glass Company (NSG) entered into a licensing agreement with the University of Sydney to commercialize the technology, resulting in the construction of a pilot production plant in Kyoto. The “Spacia” glass product was launched in 1996 and was sufficiently successful to warrant the commissioning of a second production facility in Ryugasa. During this time, a substantial increase in production efficiency was realized by sealing and outgassing the cavities through a single-stepped heating phase. Richard Collins reflected favorably on his collaboration with NSG during a presentation at Glass Performance Days in Finland in 20176. The company has continued to innovate and sell its glass products, and research efforts at the University of Sydney continue to this day.
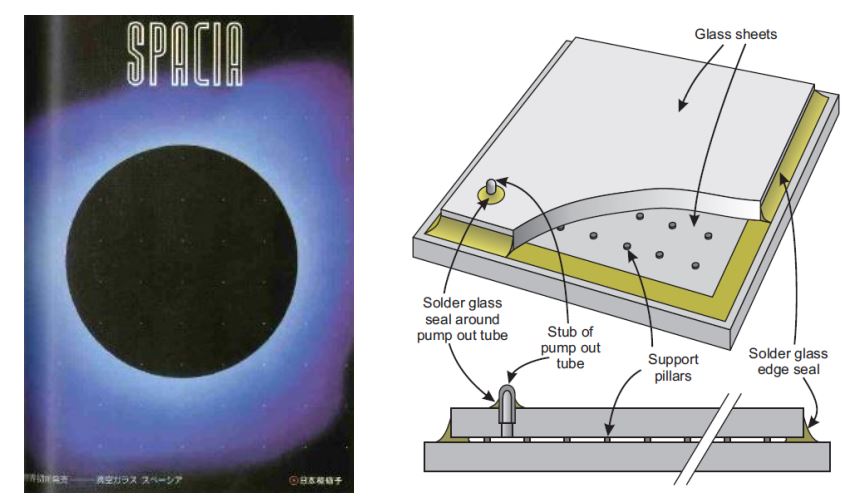
Current Market for Vacuum Insulated Glass
The market for vacuum insulation glass has evolved in recent decades as additional manufacturers have developed production capabilities. NSG still has a significant market presence. Fineo glass, an architectural product, resulted from a collaboration between Panasonic and AGC in 2018 based on technologies developed for refrigerated display cases. It became the first VIG product to earn CE certification in Europe7. Chinese manufacturers account for approximately 80% of worldwide production capacity8. Shandong Haanglass brought products to market in 2019. Synergy NA introduced its Therm glass product in 2017 after acquiring the technology from a collaboration between the University of Sydney and the Chinese Government9. Land Glass, a manufacturer of glass tempering equipment, began producing a VIG product in 2016, which, up until recently, was sold under license by VIG technologies in the United States. Recently, Vitro Glass has acquired these rights to become the new exclusive US distributor of landglass products under the trade name “Vacumax.” They plan to bring production capabilities stateside by integrating landglass fabrication equipment into their domestic production facilities10. Guardian Glass also aims to establish a market presence. An internal research program yielded the implementation of a domestic pilot production facility in 2016; however, this effort was paused after three years, citing a lack of demand. The company has launched a new effort by partnering with Danish-based Velux Group to market a new VIG product11. Luxwall, a start-up founded in 2016 in Ypsilanti, Michigan, services residential markets through a partnership with Kolbe Windows and Doors under the trade name Enthermal Glass12.
Designing with Vacuum Insulated Glass Units
The basic components of a Vacuum Insulated Glass (VIG) unit are shown in Figure 2. Special components are required to evacuate the air cavity, maintain that vacuum over time and prevent the glass lites from collapsing inward under the tremendous pressure generated. The edge seal, placed around the perimeter of the glass, can be made from various materials. Early VIG units employed high-temperature glass solder; however, “low temperature” fabrication processes have largely replaced this material with other proprietary materials such as metals, flexible gaskets and low-temperature solders. These improvements allow heat treatments applied to the glass before assembly to be maintained and reduce the energy consumption of process equipment. Small pillars are required to maintain separation of the glass lites since atmospheric pressure, approximately equivalent to the weight of a bowling ball on every square inch of glass, deflects the glass panes inward. The geometry, material and patterning of the pillars affect heat transfer since these elements act as small thermal bridges. Manufacturers must carefully analyze these parameters to balance the resilience of the assembly with thermal performance. Metals and ceramics are the most common materials used, and the array of spacing between the pillars can be greater when the glass is tempered, lowering heat transfer. Since even the highest quality glass is not perfectly flat, there is always some risk that the occasional pillar may become displaced. This reality must factor into the deployment chosen. The geometry of the pillars can be either cylindrical or spherical, and their size depends largely on their constituent material. As with edge seals, the finer details of these applications are often proprietary. Conventional assemblies include a visible evacuation port on the surface of the glass to pull an initial vacuum on the glass; however, recent advances in fabrication have yielded designs that do not require this feature. A “getter” that absorbs off-gassing over time is also typically visible, as are the support pillars when viewed close.
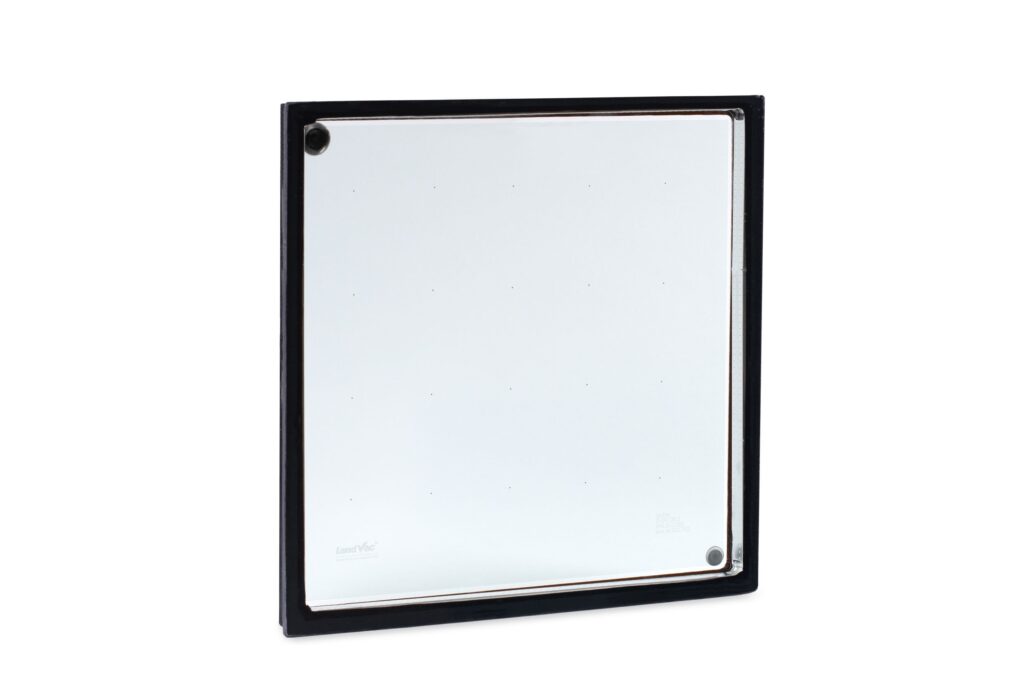
To expand upon the performance of VIGs, it is important to consider the contribution to heat transfer of each component which comprises a typical window. At the “center of glass,” as shown in Figure 4, heat flows perpendicular to the plane of glass and is not influenced by other elements. It is commonplace that heat transfer at the center of the glass is much lower than those associated with each framing component and the “edge of glass,” which is influenced by the edge spacer assembly and retention of the glass by the framing system. Notably, VIGs exhibit exceptionally low center of glass heat transfer relative to other configurations; however, heat transfer within framing systems and at the glass edge can sometimes be higher than conventional designs. The rate of heat transfer is commonly associated with the U-factor of the product Eq.1. To establish the U-factor of an entire product, conventional standards, such as NFRC100 in the United States, determine the rate of heat transfer for the various zones depicted in in Figure 4, their associated U-factors and area weights those values based on their projected area. Glass center U-factors associated with VIG products are equivalent to or better than best triple-glazed IGUs with center of glass values as low as 0.05 or R-20, which is equivalent to 5” of rock wool insulation. Losses associated with the edge are, unfortunately, much higher. Thus, while tangible improvements are realized with conventional glass, VIGs will not deliver U-factors associated with opaque wall insulation when the entire product is evaluated. This is especially true when lites of glass are small. It is also of substance that the fundamental mechanism that realizes the insulating qualities of VIGs is the elimination of conduction and convection within the cavity space. Solar radiation is subsequently not mitigated in the same manner that these assemblies reduce temperature-driven heat transfer. Fortunately, modern high-performance solar control coatings exist to combat this and can offer exceptional performance when used in conjunction with VIG.
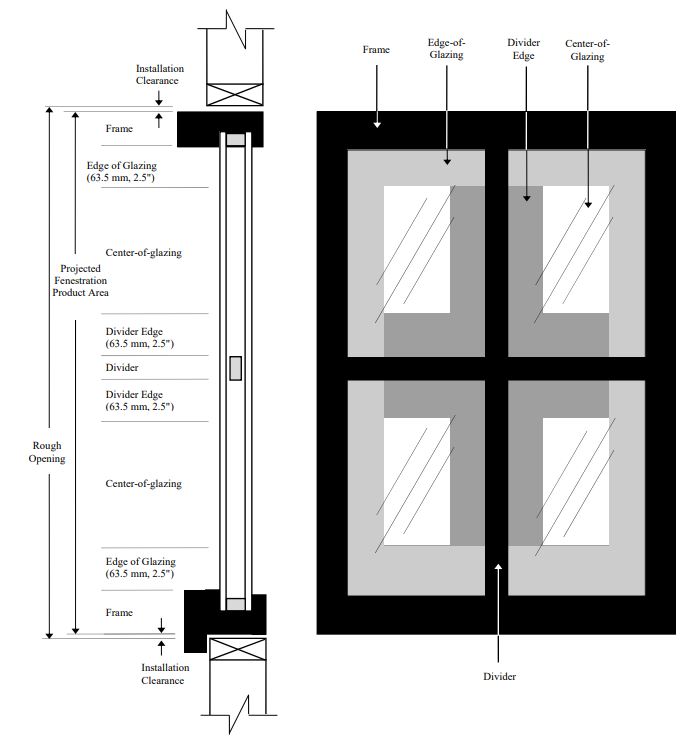
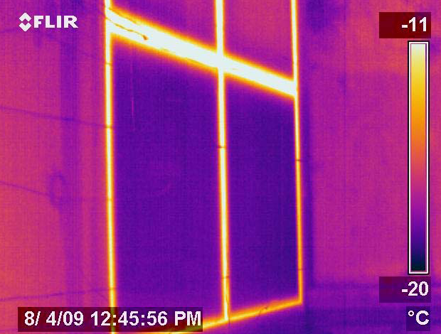
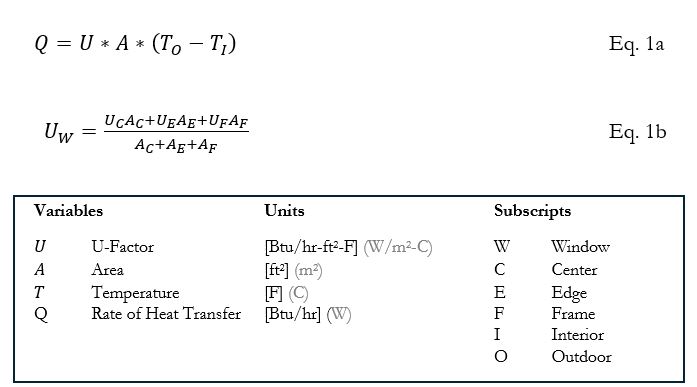
Since VIGs do not incorporate an air space, their sound attenuating properties are governed solely by structural coupling between the glass liters. Subsequently, their acoustic properties are better than those of monolithic glass of comparable dimensions. Furthermore, hybrid VIGs perform somewhat better than their insulated glass counterparts. While this benefit is unlikely to sway a given design, it provides an added benefit above simply reducing thermal transfer. VIGs invoke unique design considerations that must be carefully analyzed. Since the edge seal is commonly far more conductive than those employed in conventional insulated glass, the “cold edge” effect of VIG assemblies may result in frost or condensation at the glass perimeter during extreme cold temperatures, especially if the assembly is not deeply recessed within the framing system. Subsequently, framing systems designed to maximize the performance of VIGs may require broader sightlines when deployed in cold climates. Alternatively, “hybrid VIG products,” which combine conventional IG cavities with a VIG layer, can be employed in traditional curtainwall framing systems; however, this comes with some added expense, especially if the process involves additional fabricators. Both thermal gradients and the rigid nature of the edge assembly require careful structural evaluation. Engineering standards that dictate the quality and design of VIGs are not as mature as those corresponding to insulated glass, which has a much longer history of widespread application. Most design professionals will quickly identify the relative infancy of many manufacturers as a potential risk. Performance values depend on parameters that are difficult to measure, such as the level of vacuum achieved, which must be taken on faith unless products are batch-tested. These hurtles are common in any innovative product and will likely be ironed out as adoption increases.
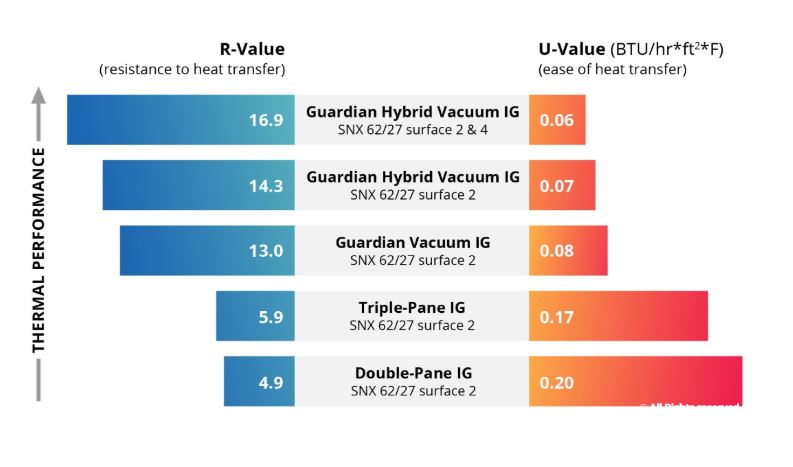
One of the greatest opportunities for VIG adoption is retrofit glazing since much of the aging building stock in the United States predates the use of wider insulated glazing units. Sustainability initiatives such as Local Law 97 in New York will likely inspire a strong demand for building improvements that retain historical elements while greatly reducing operational carbon. Previously, the best performance improvements were limited to reducing solar transfer by application of solar control films. Since VIG units are inherently slender, they fit into the glazing pockets of older systems, realizing the potential to improve solar performance and significantly reduce temperature-driven heat transfer. It is important when entertaining such efforts also to mitigate heat loss associated with air leakage, which may be substantial if seals deteriorate or for legacy aluminum systems that feature dry gasket to capture glass in place of modern two-part structural sealants, or for systems with numerous operable leafs. Angel Ayon of Ayon Studio Architecture and Preservation presented a case study of a 28-story VIG retrofit installed at 310 Riverside in Manhattan at the Facade Tectonics World Congress in 202413.
Building Integrated Photovoltaics
Like VIG, building integrated photovoltaics (BIPV) is not an infant technology. Simple deployments, such as those featuring arrays of conventional photovoltaic products to building rooftops, have been implemented as early as the 1970s and 1980s. The integration of photovoltaics as a glazing element began to evolve in the 1990s in Germany. In 1991, a retrofit installation of insulated PV modules was installed into the existing curtainwall of the Public Utilities Building in Aachen14. By the late 1990s, installations were being performed in the United States. Amorphous silicon panels were installed at 4 Times Square in 1999, which is regarded as the first application of vertical BIPV within curtainwall assemblies in the United States15. Since that time, various prominent buildings have included BIPV. For instance, the University of Washington Life Sciences Building completed in 2018 (Perkins+Will), which has received numerous architectural awards, such as the AIA architecture award in 2023, features a 650 square meter solar fin installation on the southwest curtainwall16.
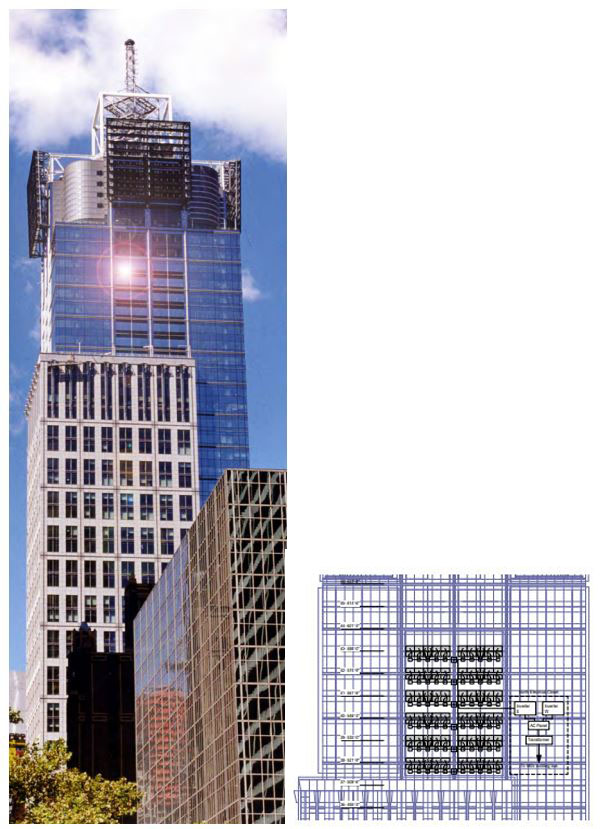
The innovation of BIPV systems provides one potential avenue to achieve net-zero buildings due to their energy harvesting potential, which offsets utility use by supplying energy back to the electrical grid. These systems employ two basic components. First, a selected photovoltaic medium is integrated into the facade in a manner that is both serviceable and achieves desired aesthetic goals. Second, the panels are interfaced by wire to a control system, which inputs the DC current from each panel to produce an aggregate AC waveform through an “inverter” or inverters that match the utility power source and supply power back to the grid. Furthermore, It is possible to design battery storage systems to store some of the power generated to offset peak energy use and provide backup power for emergencies. Whether or not this modality is employed will likely depend on whether alternate means of backup power generation are already in place. Early photovoltaic installations required panels to be installed in series whereby a single inverter serviced numerous panels; however, in this modality, power generation was limited by the effects of shading. It is a tenant of photovoltaic design that power generation is limited by the least-generating panel when panels are connected in series. Modern systems are more likely to utilize micro inverters, which service individual panels to mitigate these effects, especially given that most vertical wall surfaces are partially shaded. From a design standpoint, the building envelope is governed more heavily by the appearance of the BIPV panels and their integration with wall systems since the supporting electrical installations are not highly sensitive to panel deployment. Design considerations for the envelope are similar to dynamic glazing since electrical leads must pass through the wall system and interface with building systems. Access and serviceability of these components are important.
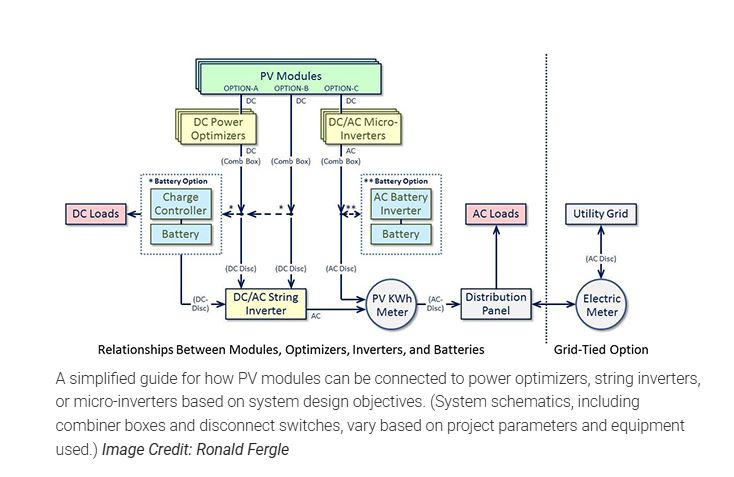
How Photovoltaic Cells Work
Photovoltaic panels are a semiconductor technology. The particle theory of thermal radiation identifies incident solar radiation as a shower of energized particles. When these particles bombard certain materials, they can separate electrons from their constituent molecules, resulting in a temporary imbalance where the electron is negatively charged and the molecule is positively charged. Left to their action they would recombine. “Doped” Semiconductors are unique since they can be tailored to contain an excess or deficiency of electrons required to achieve this balance. The simplest model of a PV cell, shown in Figure 8, includes both “p-type” and “n-type” doped semiconductors. P-type conductors are positively charged since their constituent molecules lack a valance electron. These vacancies are commonly referred to as “holes.” N-type conductors are negatively charged because they contain “free electrons,” which are not bound to atoms. When these two types of semiconductors are connected, a stable region is created at their interface since the free electrons move to fill the adjacent holes. This region, the “depletion zone” or a p-n junction, acts as a barrier preventing additional electron diffusion. As described, solar radiation has the potential to “knock electrons free” in the depletion zone. When this occurs, additional electrons and holes are ejected into the n-type and p-type semiconductors, creating a difference in charge. Much like a battery, attaching a circuit between the substrates will result in a current flow. Notably, this description is somewhat simplified; however, it provides a working illustration of how PV cells operate. A detailed discussion of every PV medium would involve a deep discussion of material sciences. The most significant performance parameter associated with a given PV product is its conversion efficiency, which measures how much incident solar power is converted to electric power. Rated values generally consider normal incidence and ideal solar conditions.
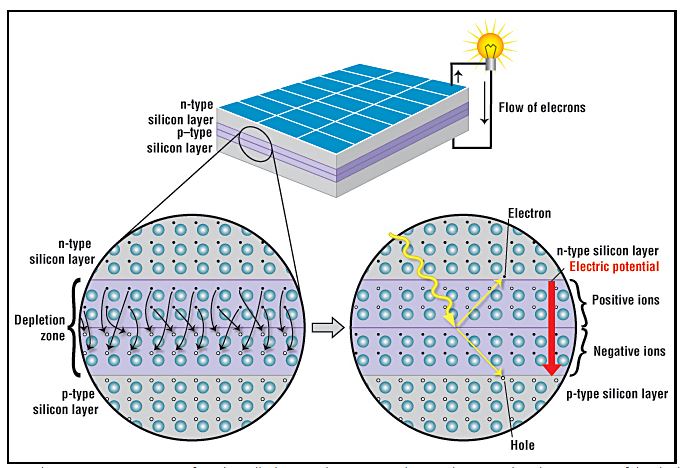
Common BIPV Materials
The energy harvesting potential of vertical BIPV is limited by several factors, including high sun angle, partial shading and the efficiency of the photovoltaic medium. The simplest and most traditional photovoltaic medium is monocrystalline or polycrystalline silicone. These materials are an abundant byproduct of electronics-grade silicone production and represent the most widely used materials for photovoltaic applications. They achieve high conversion efficiency ranging from 15-25% and are opaque. Mono-crystalline panels present a dark, uniform appearance, whereas polycrystalline panels present the familiar pattern of blue shards. Both materials are “batch processed,” which limits production efficiency. Efforts to develop lower-cost materials realized thin film technologies such as “amorphous silicon,” which exhibit lower output of 10-15% but can be manufactured on a reel-to-reel process. Other prominent thin-film technologies include Cadmium Telluride (CdTE) and Indium Gallium Selenide (CIGS). A fascinating and relatively novel class of photovoltaic media is composed of semi-transparent PV media, such as the class of Dye-Sensitized Organics, which can be applied in semi-transparent colors and patterns, providing a broad array of esthetic possibilities. Conversion efficiencies associated with this latter class of materials were initially somewhat low, but recent advances have brought performance values more in line with traditional thin films.
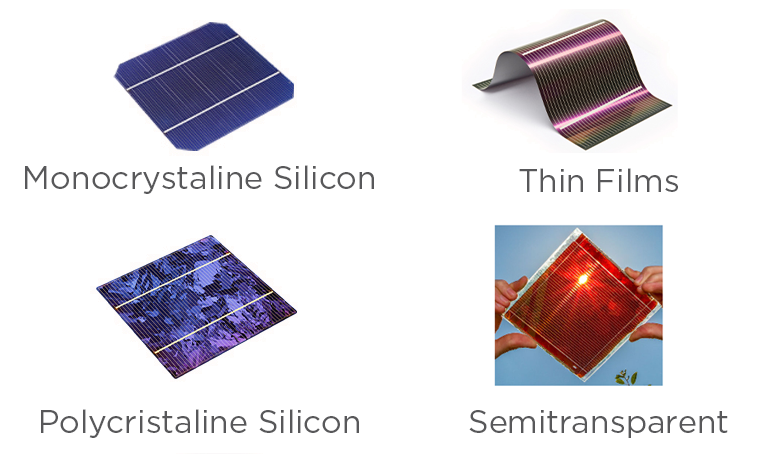
Market for BIPV Glazing
Most of the world’s leading float glass suppliers offer or are working to increase the production capacity of their BIPV products, and various manufacturers are specifically dedicated to innovating BIPV technology. The past five years have witnessed a whirlwind of partnerships. Vitro Glass partnered with First Solar, a prominent US-based BIPV manufacturer, to bring their “Solarvolt” product to market in 2021 and has paused accepting new orders, citing saturated plant capacity17. Guardian Glass formed a similar partnership with Polish-based ML systems in 202018. In the same year, AGC partnered with various firms, including PHYSEE technologies, to realize “Sun Ewat”19. NSG and Pilkington partnered with Solaria in 201620 to introduce their ”sun-plus” glazing product. Saint Gobain joined with Megasol in 202221. Other market players include Onyx Solar, Mitrex, SoliTek, Envelon, Solarlab, Hanergy, Hiitio and many others.
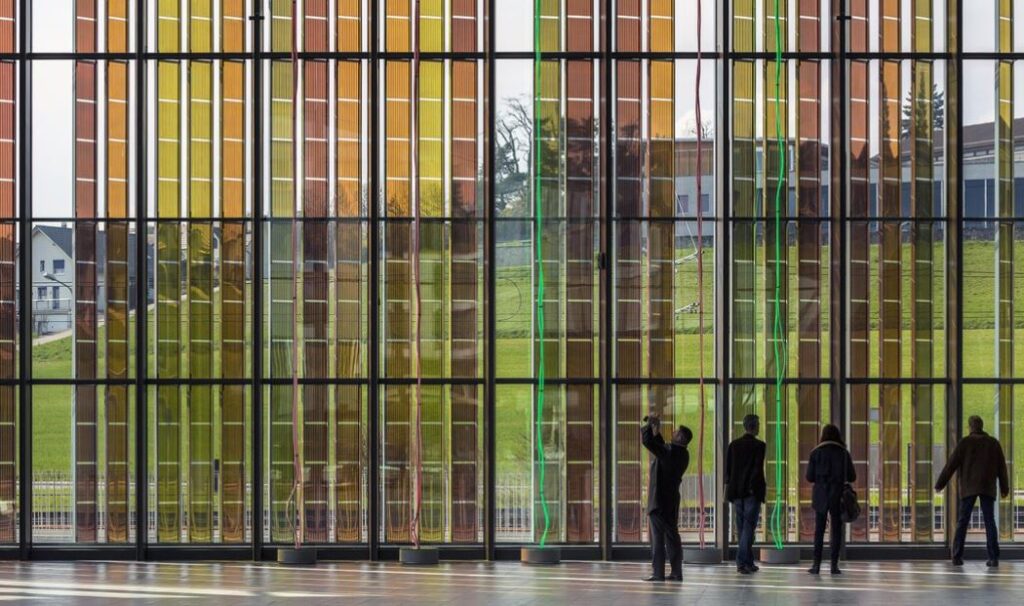
Significant research has also been applied to developing more complex products that overcome the barriers associated with vertical applications. These systems commonly employ prisms and various optical mechanisms to re-direct solar radiation to improve efficiency or create configurations that maintain daylighting. Research initiated as early as 1970 has considered luminescent solar concentrators (LSCs) to act as a waveguide, collecting solar energy over the surface of a pane of glass and directing it towards the perimeter of the lite in the glass plane. Other designs have employed arrays of prisms to re-direct solar incidence into photovoltaic slips oriented out of plane with the field of vision22. The published literature testifies to these research efforts. A review paper by B.S. Richards and I. A. Howard, published in Energy and Environmental Science in 2023, considered 140 works dedicated to the application of LSCs in BIPV applications23.
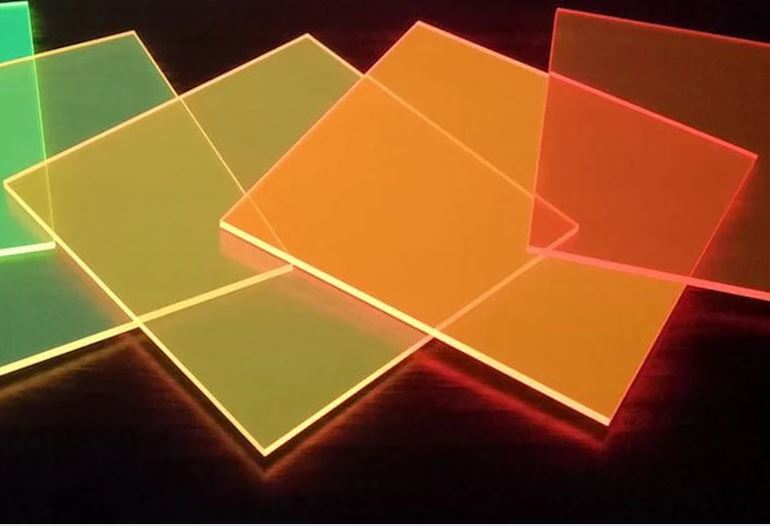
Conclusion
This article highlights how glazing innovations redefine the relationship between buildings and energy use. Once limited to providing weather protection and daylight, glazed wall systems now serve as high-performance thermal barriers, dynamic environmental responders, and even energy generators. In the next installment, we will explore how advanced glazing products balance the tradeoffs between embodied carbon and operational carbon reduction, further advancing sustainable building practices.
- Wikipedia. “James Dewar” Wikipedia, https://thermos.com/pages/history, 2024 ↩︎
- Thermos Brand. “History of Thermos” Thermos website, https://thermos.com/pages/history 2024 ↩︎
- A. Zoller, Hohle Glassscheibe “German Patent Application No. 387655.” 1913 ↩︎
- S.J. Robinson and R.E. Collins, Proceedings of ISES Solar World Congress, Kobe, Japan (1989) p. 1079-1083 ↩︎
- R. Collins, Vacuum Insulation Glass – Past, Present and Prognosis, Glass Performance Days, Tampere Finland, June 28-30th, 2017 ↩︎
- R. Collins, Vacuum Insulation Glass – Past, Present and Prognosis, Glass Performance Days, Tampere Finland, June 28-30th, 2017 ↩︎
- “Fineo is now the only vacuum insulation glass with CE Marking” GW News, https://www.gw-news.eu/glass/agc-fineo-now-only-vacuum-insulation-glass-ce-marking, 2024 ↩︎
- N. Dick, “Next Step in VIG: Planning for Growth” Glass Magazine, https://www.glassmagazine.com/article/next-step-vig-planning-growth, 2024 ↩︎
- “Synergy NA LLC Company Profile” Glass Open Book, https://glassopenbook.com/id201768, 2024 ↩︎
- “Vitro Acquires Exclusive Rights to Sell Tempered Vacuum Insulated Glazing Unites” USGlass, https://www.usglassmag.com/vitro-acquires-exclusive-rights-to-sell-tempered-vacuum-insulating-units/, 2021 ↩︎
- “Guardian Glass, Velux Partner to Develop Tempered VIG, USGlass, https://www.usglassmag.com/guardian-glass-velux-partner-to-develop-tempered-vig/ 2024 ↩︎
- “Luxwall Partners with Window Company to Distribute VIG” USGlass, https://www.usglassmag.com/luxwall-partners-with-window-company-to-distribute-vig/ , 2024 ↩︎
- A. Ayon, “Reglaze or Replace” Facade Tectonics Institute World Congress, Salt Lake City, UT 2024 ↩︎
- F. Crassard and J. Rode, “The Evolution of Building Integrated Photovoltaics (BIPV) in German and French Technological Innovation Systems for Solar Cells” Master of Science Thesis in Economics and Innovation, Chalmers University of Technology, Goteborg, Sweden 2007 ↩︎
- P. Eiffert, G. Kiss, “Building-Integrated Photovoltaic Designs for Commercial and Institutional Structures; A sourcebook for Architects, US Department of Energy, 2000 ↩︎
- Onyx Solar, “Life Sciences Building” Onyx Website, https://onyxsolar.com/the-life-science,2024 ↩︎
- “Vitro and First Solar Expand Contract” Glass Magazine, https://www.glassmagazine.com/news/2023/vitro-and-first-solar-expand-contract, 2023 ↩︎
- “ML System signed a strategic partnership agreement with guardian glass” PV Magazine, https://www.pv-magazine.com/press-releases/ml-system-signed-a-strategic-partnership-agreement-with-guardian-glass/ , 2020 ↩︎
- AGC Glass Europe. “AGC Glass Europe Presents SunEwat: a new range of energy-generating facade solutions for all your need” AGC Glass Europe Website, https://www.agc-glass.eu/en/news/press-release/agc-glass-europe-presents-sunewat-new-range-energy-generating-facade-solutions, 2020 ↩︎
- Pilkington. “The NSG Group and Solaria Announce Collaboration” Pilkington Website, https://www.pilkington.com/en/global/news-insights/latest/the-nsg-group-and-solaria-announce-collaboration , 2016 ↩︎
- Saint Gobain. “Saint-Gobain extends its sustainable solutions offer for facades in Europe by investing in building integrated photovoltaics” Saint Gobain Glass Website, https://www.saint-gobain.com/sites/saint-gobain.com/files/media/document/20220928_Megasol_VA.pdf 2022 ↩︎
- D. Baker, “Pythagoras Solar Windows and Energy Breakthrough” SFGate, https://www.sfgate.com/tech/article/pythagoras-solar-windows-and-energy-breakthrough-2366579.php, 2011 ↩︎
- B.S. Richards and I.A. Howard, “Luminescent solar concentrators for building integrated photovoltaics: opportunities and challenges” Energy Environ. Sci, 2023, 16, 3214-3239 ↩︎