By Dan Bettenhausen, Director of Mechanical Engineering & Adam Krueger, Mechanical Engineer
This is the second article in a series exploring advances in glazing products, focusing on thermal performance and sustainable design. The first article examined conventional insulated glazing products—prevalent in new construction due to energy codes—highlighting the scientific principles behind their performance and recent advancements in coating technology. While effective, these products do not represent the peak of thermal performance available today. To enable greater architectural freedom, improve occupant comfort, reduce maintenance needs, and address alternative goals like sound attenuation, new technologies have evolved that build on traditional insulated glazing units. This article explores commercially available yet underutilized innovations, including multi-layer glass systems and dynamic tinting technologies.
Triple Glazing

Since the width of the cavity in an insulated glazing unit does not correlate linearly with thermal resistance and decreases for dimensions exceeding one-half of an inch due to the action of convection, there is an upper bound on the R-value that can be achieved for a traditional assembly consisting of just two lites. To achieve further enhancement, partitions must be introduced to produce a series of cavities that do not individually exceed this threshold width. During the 1980s and 1990s, various efforts were made to market a “triple IG”. Southwall Technologies introduced a “heat mirror” in the 1980s, which ambitiously employed layers of plastic film suspended within the glazing cavity. This was no small manufacturing feat, given that the technology employed multiple edge spacers to constrain the film. The propensity of the film to become distorted by cavity pressures, forces exserted by framing systems, and other factors also presented manufacturing challenges. While the product exhibited excellent performance, with R-values as high as R-20, its widespread innovation was curtailed by lawsuits, market perceptions, and high costs1. It is also significant to note that up until the late 2000s, after a series of corporate acquisitions and eventual ownership by Eastman, the product lacked a true “structural seal,” which limited its use to residential applications where it served to fill a niche market for ultra-high performance glazing. Eastman eventually succeeded in bringing a commercial product to market in 2010 but later chose to cease glass fabrication after just five years, citing a lack of demand23. In 1991, Lawerence Berkley National Laboratory (LBNL) experimented with glass make-ups that included a thin intermediate lite, primarily to retrofit the glass into framing systems with glazing pockets sized for conventional IGs. Despite providing an enhanced performance potential, glass manufacturers failed to adopt the technology, citing a lack of initiatives and manufacturing complexities4. Commercialization efforts have remained dormant until just recently. Subsequently, the first triple pane glass offered for commercial applications employed standard lite widths, resulting in relatively bulky assemblies. Such make-ups were first marketed in Europe during the same time frame and were later adopted in the United States. Currently, they represent the most common form of triple glazing used in commercial applications. Figure 1 displays various triple-glazed make-ups.
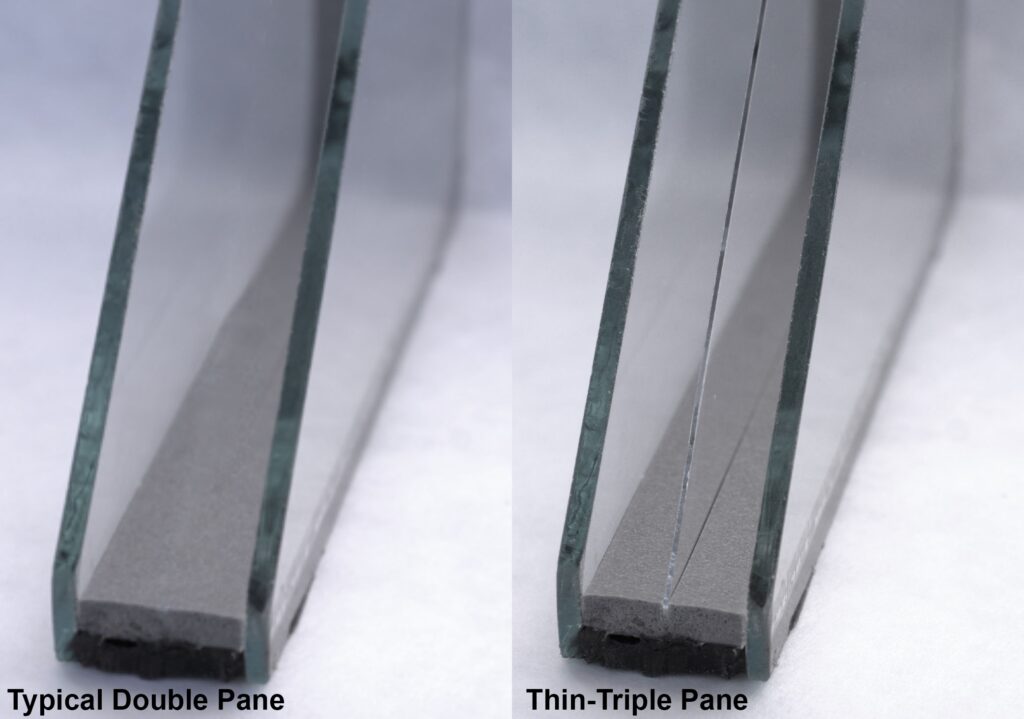
The increased mass of conventional glass widths in triple-glazed assemblies enhances acoustic performance—a common reason for their use—but their added weight and depth demand heavier framing and more complex structural designs. Both factors increase the cost of triple glazing and slow its proliferation. Growing industry focus on sustainable design also imposes challenges since adding glass and aluminum to products greatly increases their embodied carbon. For these reasons, it is unsurprising that renewed focus is being given to triple-glazed assemblies that diminish the use of these materials. In 2019, LBNL once again conducted a research study with various window manufacturers to investigate the use of thin glass in triple-pane assemblies since parallel markets have evolved for the material related to the production of cell phones and tablets. The study evaluated the thermal performance characteristics of windows employing the technology and their potential impact on annual energy use5. Furthermore, the lab partnered with Anderson Windows and Alpen to develop a residential product6. In the commercial sector, Corning recently engaged in a significant process development effort with glass fabrication equipment manufacturers to enable the use of their ”Advanced Thin Glass (ATG)” product within glazing assemblies7.
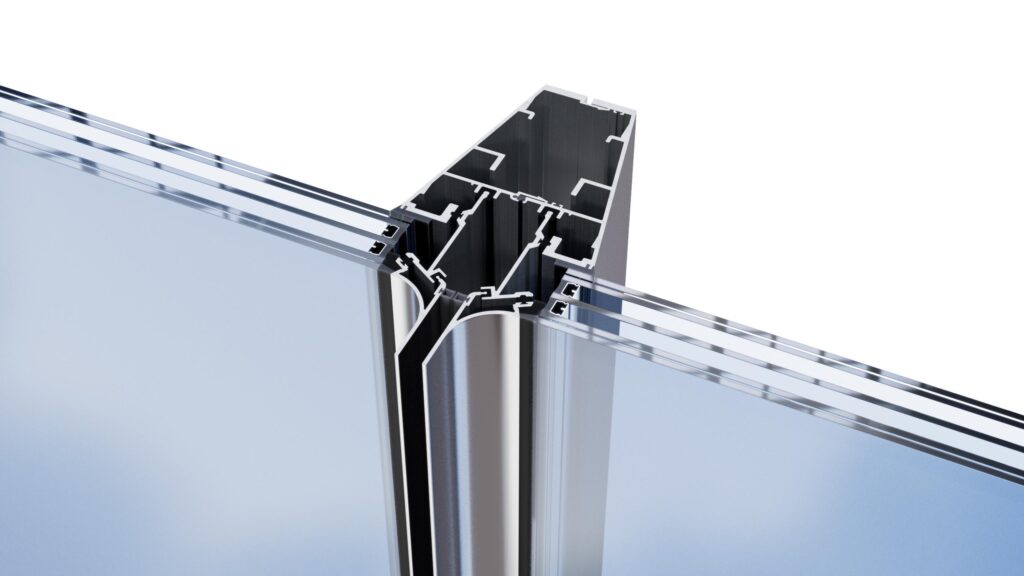
Introducing a third lite to a glazed assembly increases the number of possible configurations that can be deployed and also impacts the esthetic qualities of the glass. For instance, cavity widths can be consistent or varied to achieve acoustic benefits, and the placement of laminates and coatings can be applied to more surfaces. Subsequently, the resultant appearance of the total assembly becomes somewhat more complicated to predict. Table 1 indicates performance values associated with various IG make-ups, including conventional IGs, employed for commercial applications to illustrate the spectrum of performance values that can be practically obtained. R-values generally range from R-3 to R-8, and up to 60% of the incident solar load can be mitigated without substantially reducing transparency. Darker configurations can achieve much greater solar rejection while still achieving some daylighting effect. It is important to remember that engineering standards determine these values and correspond to the environmental parameters specified by those procedures, including temperatures, wind velocities, free convection effects, and solar incidence angles. In fact, the solar spectrum of incident radiation is defined. Furthermore, they only partially appreciate building space conditioning parameters that affect convective heat transfer and local temperatures.

Electrochromic Glazing
Dynamic glazing, also referred to as smart glass, switchable glass, smart-tinting glass, or chromogenic glazing, stems from initial research published by Swedish material physicist Claes-Goran Granqvist, a researcher at Chalmers Institute of Technology in Sweden, who collaborated with Carl Lampert at LBNL in the United States, and Jim Stevens of the University of Guelph in Canada among other colleagues during the 1980s8. They aimed to conceptualize a glass product with an adjustable tint to reduce solar loads selectively. After considering thermochromic and photochromic mechanisms, he focused his research on electrochromic coatings using tungsten-doped vanadium dioxide to achieve this aim. In the subsequent decade, after publishing several studies, he collaborated with a former Ph.D. student, Tord Eriksson, to commercialize the technology. This effort did not result in significant business growth due to changing sentiments toward energy conservation and the emergence of competing technologies. Funding for research efforts dried up throughout the 1990s, and it was not until ten years later, with the founding of Chromogenics in 2003, that a commercial venture would make successful use of his research8. In the United States, another business enterprise was initiated by John Van Dine, a chemical engineer from Rutgers University. In 1989, he founded Sun Active Glass Electrochromics (SAGE) in Valley Cottage, New York. By the late 1990s, this venture had progressed from a conceptual research collaboration with Rutgers University to developing a manufacturing facility in Faribault, Minnesota, which began commercial shipments in 20039. This effort further benefited from an offer for funding from the United States Department of Energy in 2010 totaling nearly 100 million dollars, which was applied to producing a new larger manufacturing facility. Shortly after that, Saint-Gobain acquired the company, which contributed research and manufacturing expertise in addition to shoring up the company’s finances10. Saint-Gobain was not alone in its aspirations to gain market share in this evolving industry. Solardigm, later branded as VIEW, developed a comparable technology in 2006, which amassed an impressive amount of startup capital totaling nearly two billion dollars from numerous investors, including Corning Glass, prior to the company’s first public offering in 2021. Unfortunately, what appeared to be a trajectory for unprecedented success resulted in bankruptcy filings three years later due to many factors influenced by lawsuits, business practices, and post-pandemic market conditions. The company will continue to operate while being restructured by private investors11.
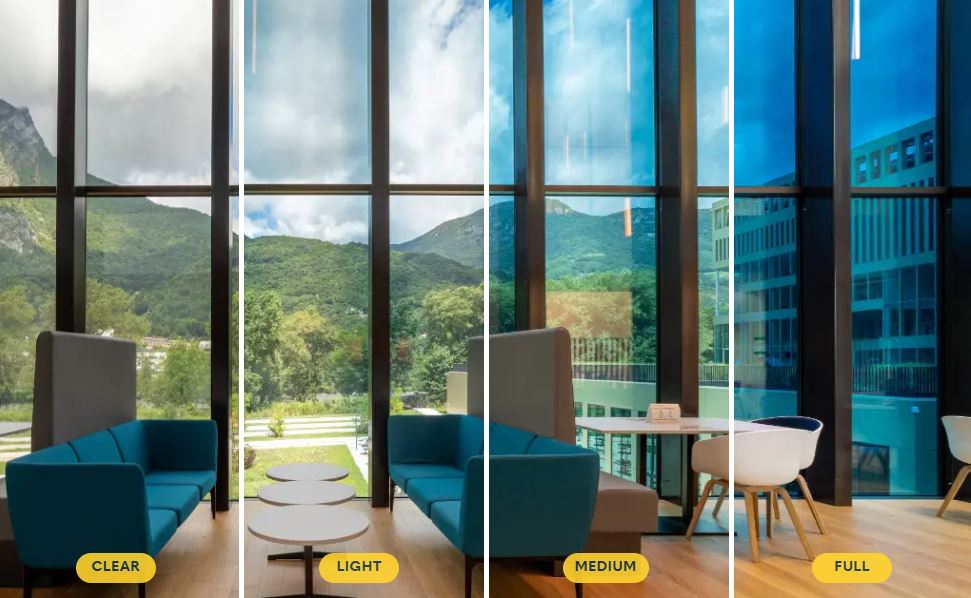
In recent years, Halio Glass, formerly known as Kinestral Technologies, also succeeded in bringing products to market. The company was founded in 2010 by Howard Turner, a chemist from Massachusetts Institute of Technology, and Sam Bergh, an Engineer from UC Santa Barbra, as a spin-off of Symyx hardware, which they mutually acquired after spending their post-academic careers in related industries. The company initially entertained a partnership with AGC Glass in 201712. In 2021, subsequent partnerships with Viracon Glass and Marvin Windows were also announced, followed by a partnership with Glassbel in 20231314. Less conventional technologies, such as Suspended Particle Device (SPD) film, developed by Research Frontiers, have been adapted from applications in transportation to architecture. Israeli-based Gauzy offers architectural products using SPD technology under license15. Companies such as Miru, Tynt, and Ambilight are also working towards establishing marketable products.
While electrochromic coatings encompass various technologies, those most used in architecture employ transparent conductors to provide a conduit for sustaining chemical reactions over the surface of the glass. The application of a small difference in voltage between the conductors, for a relatively short period, causes positively charged lithium ions to flow along the voltage gradient between substrates in a manner that affects their optical behavior. An electrolyte is generally “sandwiched” between oxide layers such as tungsten oxide and nickel oxide, which serve as the electrochromic medium and doped ion source, respectively. When the electrochromic layer is saturated with ions, it undergoes a redox reaction, resulting in light absorption and attentive opacification. Since the reaction occurs progressively, various tint levels can be achieved, as shown in Figure 3. When ions are pushed back to the source by reversing the voltage potential, the tungsten oxide layer becomes transparent again, which is in its natural state. Notably, the voltage only needs to be maintained during the transition process. The electrochromic medium remains “locked” in a stable state without electric potential. This process is shown in Figure 4.
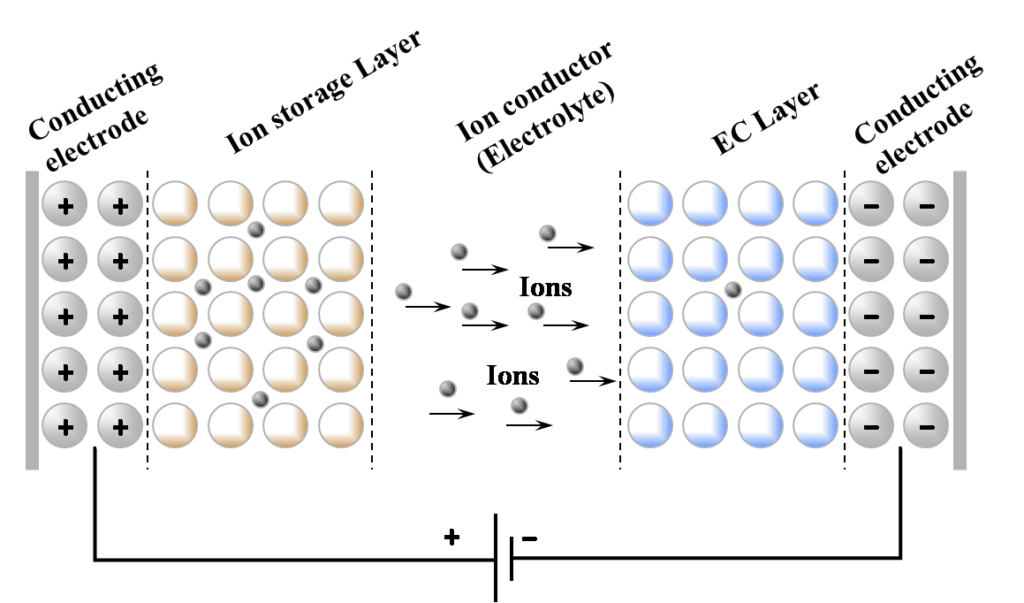
Electrochromic glass is not energy-intensive since the power consumed to alter the glass state is only applied intermittently, employing low voltages. Furthermore, electrochromic glass can overcome certain obstacles associated with conventional interior shading devices. For instance, since energy is absorbed in the glass’s outboard lite, the solar gain reduction will be much higher than that achieved by conventional interior blinds, which primarily block glare while still allowing solar energy to pass through the glazing and into the building. Electrochromic glass is easily integrated with control systems to adjust to dynamic weather conditions in real-time. It is well known that a major shortcoming of conventional shading systems is that energy savings are not realized when they are left open in unoccupied spaces or ignored by occupants. Electrochromic glass lends itself to applications where traditional blinds may be impractical to install, such as atriums with large expanses of glass. Emerging electrochromic products allow tinting to be applied as a gradient, which limits high-angle sun while preserving views and daylight. Among these advantages, it is difficult to deny that a certain visceral quality is imparted by the sleek, uncluttered look of the application that preserves exterior views and is visually appealing.
While these benefits seem tantalizing initially, they are not without compromise. Electrochromic systems are significantly more expensive to install than conventional glass, requiring wiring to be placed within framing systems and coordinated with building electrical systems16. Warranty periods encompassing the electrochromic function of the windows may be less than those of conventional glazing systems, which are attended by a perception that passive products are less likely to be problematic after their warranty periods expire. Furthermore, long-term serviceability is challenged by the fact that the range of appearances generated by the dynamic behavior of a given product is specific to the technology employed by the manufacturer and may involve proprietary control systems that are not conducive to replacement. It is noteworthy that even in the “off state,” most products impart a hue on the glass that must be coordinated with desired esthetics. Other concerns mirror those that would apply to any innovative technology, such as limitations associated with the number of manufacturers with an established production history, available sizes, and lead times.
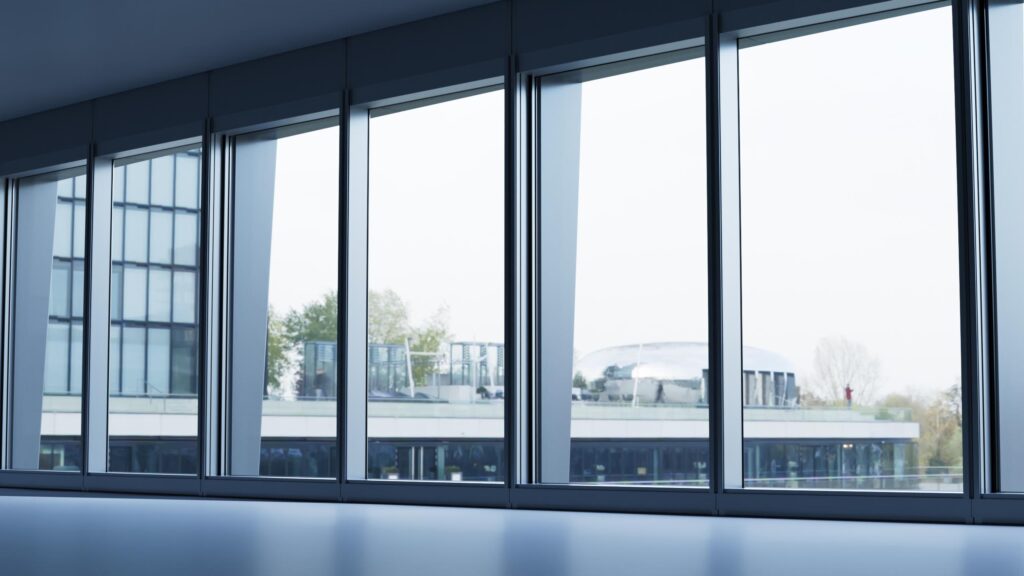
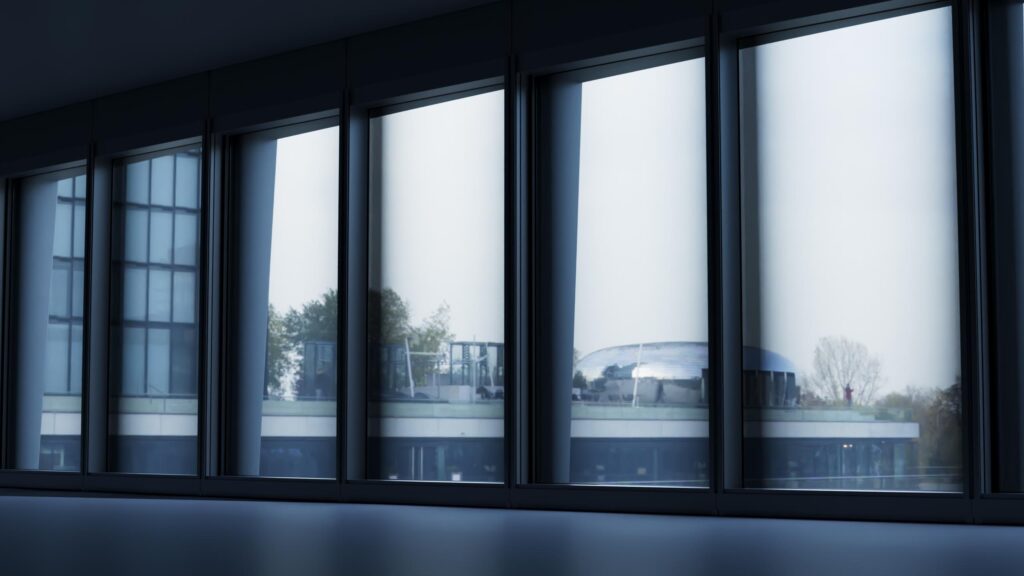
Thermochromic Glass
Thermochromic glazing is similar to electrochromic glazing in that it exhibits dynamic opacity to control solar gain and glare; however, the mechanism by which this behavior is accomplished differs. Whereas electrochromic glazing requires a voltage source to initiate a transition between states, thermochromic glazing varies its tint by the temperature of the glazing. This behavior can be accomplished with either inorganic or organic compounds. A common inorganic compound is the transition metal vanadium dioxide, which naturally undergoes transition near room temperature. Certain organic polymer compounds, similar to those used for novelty products such as mood rings and t-shirts, have also been employed over temperatures suitable for thermochromic glass17. For example, the “Ligand Exchange Thermochromic System (LETC),” developed by Pleotint 18. The fundamental mechanism that facilitates the change of optical state in a thermochromic medium is the alteration of the geometric structure of the molecules in a manner that affects light refraction. For instance, Vanadium dioxide transitions between monoclinic to tetragonal rutile at sixty-eight degrees centigrade. Doping the material with tungsten lowers the transition temperature, allowing for the range of temperature transition to be somewhat tailored.
Thermochromic glazing represents a compromise between electrochromic products and conventional solar control coatings in that it is passive and does not require any special maintenance provisions, electrical wiring, or controls. Only the costs inherent to manufacturing represent a departure from other products manufactured on vast scales. The price for this efficiency is the level of control that can be exacted upon the tint exhibited at any moment, which may not be suitable for applications where transparency or opacity are desirable, independent of the environmental conditions. For instance, during periods of cold winter, there may be no glare reduction, requiring conventional shades. In other instances, occupants may desire opacity or transparency according to their needs for privacy and exterior views.
The market for thermochromic products has been slower to evolve than their electrochromic counterparts due to the limitations described. During the mid to late 2000s, companies like Ravenbrick and Pleotint sought to manufacture applied films and laminates. Pleotint, started by Harlan Byker received a grant from the United States Department of Energy in 2010 to pioneer a manufacturing process for LETC film. A partnership forged with PPG, now Vitro, one year later further refined the process for full-scale production. The “Suntuitive” line of products, which combined thermochromic employing LETC with conventional low-e coatings, entered production not long after that but has temporarily ceased production, citing post-pandemic market conditions1920.
Performance values attained by dynamic glazing products vary somewhat from product to product; however, control of glare and solar gain are the primary benefits. U-factors may be slightly higher than equivalent make-ups with traditional low-e. Recall that “low-e” corresponds to the “emittance” of the coating applied within the glazing cavity, and differences exist between most electrochromic technologies and traditional coatings. Achieved reductions in solar gain net a greater benefit than the minor increase in U-factor; however, this reality should be entertained when determining project specifications. Some manufacturers offer an additional solar control coating to improve the U-factor opposite of the EC surface. Values corresponding to a traditional product produced by SAGE are shown in Figure 5. Figure 6 indicates values corresponding to a thermochromic assembly published by Suntuitive.
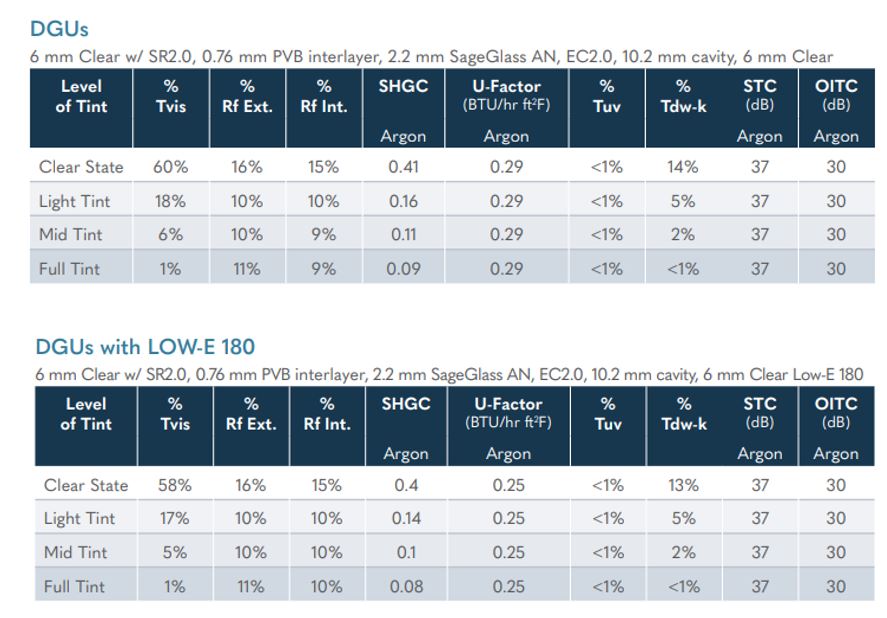
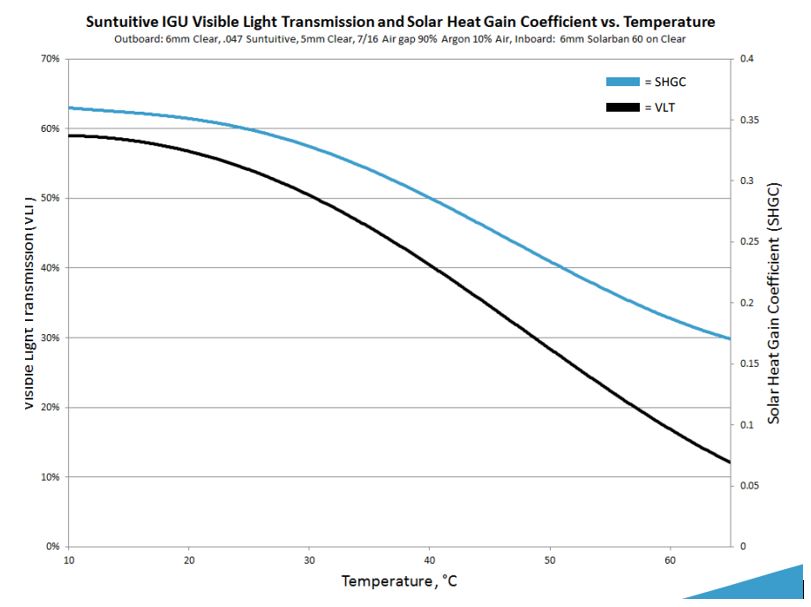
Figure 6: Solar and Optical Properties of Thermochromic Glass versus Temperature for a Conventional Insulated Glazing Unit produced by Suntuitive | Source: Suntuitive
Summary
This article expanded on the thermal performance of glazing products, exploring advancements in manufacturing technologies and the scientific principles behind their functionality, focusing on widely produced solutions. Future articles will delve into emerging technologies like Vacuum Insulated Glazing (VIG) and Building Integrated Photovoltaics (BIPV), while also addressing the balance between embodied and operational carbon.
- Scott Gibson, Insulating Glass Keeps Getting Better, Fine Home Building Magazine, December 2020/2021 ↩︎
- https://www.buildinggreen.com/blog/heat-mirror-structural-sealant-glazings ↩︎
- https://www.usglassmag.com/eastman-to-shutter-southwall-insulating-glass/ ↩︎
- https://www.greentechmedia.com/articles/read/triple-glazed-super-window-builds-on-decades-of-government-research ↩︎
- Thermal performance and potential annual energy impact of retrofit thin-glass triple-pane glazing in US residential buildings. ↩︎
- https://newscenter.lbl.gov/2018/06/06/super-window-could-save-billions-in-energy-costs/ ↩︎
- https://www.corning.com/worldwide/en/innovation/corning-emerging-innovations/glass-for-advanced-windows.html ↩︎
- M. M. Anderson, B.A. Sanden and C. Palmberg, Green Nanotechnology in Nordic Construction, Eco-inovation Strategies and Dynamics in Nordic Window Value Chains. Nordic Innovation Center, Olso Norway p. 66-67 ↩︎
- Window Technology, National Institute of Standards and Technology,Advanced Technology Program Status Report ↩︎
- https://www.twincities.com/2012/05/08/faribault-based-sage-electrochromics-sold-to-french-industrial-firm/ ↩︎
- https://www.forbes.com/sites/davidjeans/2023/07/10/view-smart-glass-softbank/ ↩︎
- https://www.agc.com/en/news/detail/1196307_2814.html ↩︎
- https://www.prnewswire.com/news-releases/marvin-halio-inc-announce-exclusive-agreement-to-bring-halio-smart-glass-to-residential-market-301267637.html ↩︎
- https://halioinc.com/ecosystem/glass-partners/ ↩︎
- Glass on Web, Gauzy Ltd. Showcases SPD technology for architectural and automotive applications at glasstec, https://www.glassonweb.com/news/gauzy-ltd-showcases-spd-technology-architectural-and-automotive-applications-glasstec, 2018 ↩︎
- https://www.smithsonianmag.com/innovation/what-will-it-take-for-smart-windows-to-go-mainstream-180980226/ ↩︎
- G. A. Niklasson and C. G. Granqvist, Thermochromic Vanadium Oxide Thin Films: Electronic and Optical Properties, Journal of Physics: Conference Series 559 (2014) ↩︎
- H.J. Byker, P.H. Ogburn, Et. Al, United States Patent US-2009283728-A1: Ligand Exchange Thermochromic, (letc), systems, NIH National Library of Medicine, 2006 ↩︎
- PPG Industries, PPG, Pleotint renew marketing alliance for SUNTUITIVE, SOLARBAN glasses, PPG Newsroom, https://news.ppg.com/press-releases/press-release-details/2014/PPG-Pleotint-renew-marketing-alliance-for-SUNTUITIVE-SOLARBAN-glasses/default.aspx, 2014 ↩︎
- SUNTUITIVE, www.sunintuitiveglass.com, 2024 ↩︎